The world of CNC (Computer Numerical Control) machining is vast and intriguing, filled with innovations that have transformed manufacturing processes across diverse industries. One aspect that often goes unnoticed yet holds substantial importance is the concept of "CNC taboo." This term encapsulates the challenges, misconceptions, and under-discussed practices within CNC machining that can significantly impact efficiency and output quality. Understanding these taboos is essential for anyone aiming to master CNC operations and leverage its full potential for precision manufacturing.
When delving into CNC taboo, one must consider the intricacies involved in machine programming, tooling, and material handling, all of which play crucial roles in shaping the final product. Missteps in these areas can lead to costly errors, machine damage, or compromised safety standards. Consequently, addressing CNC taboo requires a blend of technical expertise, practical experience, and a willingness to challenge conventional practices to optimize CNC machining processes.
Moreover, CNC taboo extends beyond technicalities, touching upon the cultural and ethical dimensions of manufacturing. Questions about data security, proprietary technology, and labor displacement surface as CNC technology continues to evolve. By exploring these facets, professionals can navigate the complexities of CNC machining with a more comprehensive understanding, fostering innovation while adhering to best practices and ethical standards.
Read also:The Modern Perception Of A Trophy Wife A Comprehensive Analysis
Table of Contents
- Understanding CNC Machining
- What is the Significance of CNC Taboo?
- Common Misconceptions in CNC Machining
- How Do CNC Taboos Impact Product Quality?
- Overcoming Programming Challenges
- Tooling Strategies to Avoid CNC Taboos
- Material Handling Best Practices
- Ethical Considerations in CNC Machining
- Is Data Security a CNC Taboo?
- Addressing Labor Displacement Concerns
- The Future of CNC Machining
- How to Innovate Without Crossing the Taboo Line?
- Frequently Asked Questions
- Conclusion
Understanding CNC Machining
CNC machining refers to the automated control of machining tools through a computer. It involves the use of computer-controlled machines to perform precise cuts, drilling, and other manufacturing processes. This method has revolutionized the manufacturing industry, providing unparalleled accuracy and efficiency in product creation.
The essence of CNC machining lies in its ability to produce complex parts with minimal human intervention. This is achieved by programming machines to follow detailed designs and specifications, which ensures consistency and precision. The versatility of CNC machines allows them to work with a wide range of materials, including metals, plastics, and composites.
There are several types of CNC machines, each serving a specific purpose. For instance, CNC mills are used for cutting and drilling, while CNC lathes are ideal for shaping cylindrical parts. Other machines, such as CNC routers and plasma cutters, further expand the capabilities of CNC technology by offering specialized functions.
Despite its advantages, CNC machining is not without challenges. The complexity of programming and the need for skilled operators can pose significant barriers to entry for some businesses. Additionally, the initial investment costs for CNC machinery can be substantial, which may deter smaller enterprises from adopting this technology.
What is the Significance of CNC Taboo?
The term "CNC taboo" encapsulates the hidden challenges and misconceptions that can arise in CNC machining operations. These taboos are often overlooked or misunderstood, leading to inefficiencies, increased costs, and potential safety risks. Therefore, recognizing and addressing these taboos is crucial for optimizing CNC processes and achieving high-quality results.
One significant aspect of CNC taboo is the tendency to rely heavily on default machine settings and generic programs. While these may work for basic tasks, they often fall short in more complex applications, resulting in suboptimal performance. Customizing machine settings and programs to fit specific projects can greatly enhance efficiency and accuracy.
Read also:Vxi Global Solutions Your Partner For Business Success
Furthermore, CNC taboo includes the reluctance to invest in proper training and education for operators. Skilled operators are essential for maximizing the capabilities of CNC machines, yet many companies underestimate the importance of continuous training. Investing in education and skill development can lead to better machine handling and fewer errors.
Lastly, CNC taboo encompasses the ethical considerations surrounding data security and proprietary technology. As CNC machines become more connected and integrated into digital networks, the risk of data breaches and intellectual property theft increases. Addressing these concerns is vital for protecting sensitive information and maintaining competitive advantages.
Common Misconceptions in CNC Machining
Despite its widespread use, CNC machining is often surrounded by misconceptions that can hinder its effective implementation. Understanding these misconceptions is essential for businesses and operators to fully leverage the benefits of CNC technology.
One common misconception is the belief that CNC machines are entirely autonomous. While these machines can perform tasks with minimal human intervention, they still require skilled operators to program, monitor, and maintain them. Neglecting the human element in CNC operations can lead to costly mistakes and machine downtime.
Another misconception is that CNC machining is only suitable for large-scale production. While CNC technology does excel in mass production scenarios, it is also highly effective for small-batch and custom manufacturing. The precision and flexibility of CNC machines make them ideal for producing intricate and complex parts, regardless of production volume.
Additionally, some may assume that CNC machining is prohibitively expensive. While the initial investment costs can be high, the long-term savings in labor, material waste, and production time often outweigh these expenses. By optimizing CNC processes and reducing errors, businesses can achieve significant cost savings over time.
How Do CNC Taboos Impact Product Quality?
CNC taboos can have a profound impact on product quality, affecting everything from dimensional accuracy to surface finish. When these taboos are not addressed, they can lead to defects, rework, and customer dissatisfaction.
One way CNC taboos impact quality is through improper tool selection and maintenance. Using the wrong tools or failing to maintain them can result in poor cuts, increased tool wear, and ultimately, inferior product quality. Regular tool inspections and maintenance are essential for ensuring optimal performance and product quality.
Programming errors are another common cause of quality issues in CNC machining. Mistakes in code can lead to incorrect tool paths, resulting in dimensional inaccuracies and surface defects. Thoroughly reviewing and testing programs before production can help prevent these errors and ensure high-quality output.
Moreover, CNC taboos related to material handling can also affect product quality. Improper storage, handling, or selection of materials can introduce contaminants or defects that compromise the final product. Implementing strict material handling protocols and quality control measures can mitigate these risks.
Overcoming Programming Challenges
Programming is a critical aspect of CNC machining, and overcoming programming challenges is essential for achieving efficient and accurate operations. By addressing common programming issues, businesses can optimize their CNC processes and improve overall productivity.
One common challenge in CNC programming is the complexity of creating accurate tool paths. These paths must be carefully designed to ensure the machine operates efficiently while avoiding collisions or errors. Utilizing advanced software tools and simulation programs can aid in developing precise tool paths and minimizing programming errors.
Another challenge is the need to program machines for a variety of materials and operations. Different materials require specific cutting speeds, feeds, and tool types, all of which must be accounted for in the programming process. Developing a comprehensive understanding of material properties and machining techniques is crucial for successful programming.
Additionally, the integration of CNC machines with other manufacturing systems can pose programming challenges. Ensuring seamless communication and data exchange between machines and systems is vital for efficient operations. Implementing standardized protocols and data formats can facilitate this integration and reduce programming complexity.
Tooling Strategies to Avoid CNC Taboos
Tooling is a fundamental component of CNC machining, and employing effective tooling strategies is essential for avoiding CNC taboos and optimizing performance. By selecting the right tools and maintaining them properly, businesses can enhance efficiency, reduce costs, and improve product quality.
One key strategy is to choose tools that are specifically designed for the material and operation at hand. Different materials and cutting processes require specialized tools to achieve optimal results. Consulting with tool manufacturers and suppliers can provide valuable insights into the best tooling options for specific applications.
Another important strategy is to implement regular tool maintenance and inspection protocols. This involves checking tools for wear and damage, replacing them as needed, and ensuring they are properly calibrated. Maintaining tools in good condition not only extends their lifespan but also ensures consistent performance and quality.
Additionally, optimizing tool paths and cutting parameters is essential for maximizing efficiency and minimizing tool wear. This involves carefully selecting cutting speeds, feeds, and depths of cut to balance productivity and tool life. Utilizing advanced simulation tools can aid in determining the most effective cutting parameters for specific operations.
Material Handling Best Practices
Material handling is a critical aspect of CNC machining that can significantly impact efficiency and product quality. Implementing best practices for material handling is essential for ensuring smooth operations and minimizing the risk of defects or contamination.
One best practice is to implement strict material storage and handling protocols. This includes storing materials in clean, dry environments and protecting them from contamination or damage. Proper labeling and organization of materials can also aid in efficient handling and retrieval during production.
Another important practice is to ensure proper material selection and preparation for machining. This involves selecting materials that meet the required specifications and preparing them for machining, such as cleaning or deburring them to remove any surface contaminants. This preparation can help prevent defects and ensure high-quality output.
Additionally, implementing quality control measures throughout the material handling process is essential for identifying and addressing any issues before they impact production. This can include conducting inspections and tests on incoming materials, as well as monitoring and verifying material properties during machining.
Ethical Considerations in CNC Machining
As CNC machining technology continues to advance, ethical considerations have become increasingly important in the manufacturing industry. Addressing these considerations is essential for ensuring responsible and sustainable practices that benefit both businesses and society.
One key ethical consideration is data security and the protection of intellectual property. With CNC machines becoming more connected and integrated into digital networks, the risk of data breaches and theft of proprietary technology has increased. Implementing robust cybersecurity measures and data protection protocols is vital for safeguarding sensitive information.
Another important consideration is the impact of CNC technology on the workforce. While CNC machines can enhance efficiency and productivity, they can also displace jobs and change the nature of work in the manufacturing industry. Balancing the benefits of automation with the need for skilled workers is crucial for addressing labor displacement concerns.
Additionally, ethical considerations extend to environmental sustainability and resource management. CNC machining can generate waste and consume significant amounts of energy, which can have environmental impacts. Implementing sustainable practices, such as recycling materials and optimizing energy usage, can help mitigate these effects and promote environmental responsibility.
Is Data Security a CNC Taboo?
Data security is a critical concern in CNC machining, yet it is often overlooked, making it a significant CNC taboo. As CNC machines become more interconnected and reliant on digital networks, the risk of data breaches and cyberattacks has increased, posing threats to both businesses and customers.
One major risk associated with data security is the theft of intellectual property and proprietary technology. CNC programs and designs represent valuable assets that can be targeted by cybercriminals. Protecting these assets through encryption, access controls, and secure data storage is essential for maintaining competitive advantages and safeguarding innovation.
Additionally, data security is crucial for protecting customer information and ensuring compliance with data protection regulations. Breaches of customer data can result in legal liabilities, reputational damage, and loss of trust. Implementing robust cybersecurity measures and adhering to data protection standards can help prevent these risks and protect sensitive information.
Moreover, addressing data security in CNC machining requires a comprehensive approach that involves both technical solutions and organizational policies. This includes conducting regular security assessments, providing employee training, and developing incident response plans to quickly address any security breaches.
Addressing Labor Displacement Concerns
As CNC technology advances, concerns about labor displacement have become more prominent. While automation can enhance efficiency and productivity, it can also disrupt traditional manufacturing jobs and change the nature of work in the industry. Addressing these concerns is crucial for ensuring a balanced and equitable transition to automated manufacturing.
One approach to addressing labor displacement is to invest in workforce training and education. Providing opportunities for workers to develop new skills and adapt to changing technologies can help them transition to new roles within the industry. This may include training programs in CNC programming, machine operation, and other technical skills.
Additionally, promoting collaboration between industry, government, and educational institutions can facilitate the development of training programs and support services for displaced workers. This collaboration can help ensure that training initiatives are aligned with industry needs and provide relevant skills for the workforce.
Moreover, addressing labor displacement concerns involves creating new job opportunities within the industry. As CNC technology continues to evolve, new roles and positions may emerge, such as CNC maintenance technicians, automation specialists, and data analysts. Supporting the creation of these roles can help offset job losses and promote economic growth.
The Future of CNC Machining
The future of CNC machining is poised for continued innovation and growth, driven by advancements in technology and evolving industry demands. As CNC machines become more sophisticated and integrated into digital networks, they will play an increasingly important role in modern manufacturing.
One key trend shaping the future of CNC machining is the integration of smart technologies and Industry 4.0 principles. This includes the use of sensors, data analytics, and artificial intelligence to enhance machine performance, optimize processes, and improve decision-making. By leveraging these technologies, businesses can achieve greater efficiency, flexibility, and precision in CNC operations.
Another important trend is the rise of additive manufacturing and hybrid machining processes. Combining CNC machining with additive manufacturing techniques, such as 3D printing, can enable the production of complex and customized parts with reduced material waste. This hybrid approach offers new possibilities for product design and innovation.
Moreover, the future of CNC machining will be shaped by ongoing efforts to address ethical and sustainability concerns. This includes the development of environmentally friendly practices, such as energy-efficient machines and sustainable material usage, as well as initiatives to support workforce development and address labor displacement challenges.
How to Innovate Without Crossing the Taboo Line?
Innovation is essential for advancing CNC machining technology and meeting evolving industry demands. However, it is important to innovate responsibly and avoid crossing the taboo line, which can lead to negative consequences such as ethical breaches, safety risks, and quality issues.
One key strategy for responsible innovation is to prioritize safety and quality in all CNC operations. This involves implementing rigorous testing and validation processes for new technologies and ensuring compliance with industry standards and regulations. By prioritizing safety and quality, businesses can minimize risks and protect both workers and customers.
Another important strategy is to engage in ethical decision-making and consider the broader impact of innovation on society and the environment. This includes addressing concerns related to data security, labor displacement, and sustainability, as well as promoting transparency and accountability in CNC operations.
Additionally, fostering a culture of continuous learning and collaboration can support responsible innovation in CNC machining. Encouraging knowledge sharing, cross-functional collaboration, and open communication can help identify potential challenges and solutions, ensuring that innovation efforts are aligned with industry needs and ethical standards.
Frequently Asked Questions
- What is CNC taboo?
CNC taboo refers to the challenges, misconceptions, and under-discussed practices within CNC machining that can affect efficiency, safety, and quality.
- How can CNC taboos impact product quality?
Improper tool selection, programming errors, and poor material handling can lead to defects, rework, and compromised product quality.
- What are some common misconceptions about CNC machining?
Some misconceptions include the belief that CNC machines are fully autonomous and only suitable for large-scale production.
- What ethical considerations are important in CNC machining?
Data security, labor displacement, and environmental sustainability are key ethical considerations in CNC machining.
- How can businesses address labor displacement concerns?
Investing in workforce training and creating new job opportunities within the industry can help address labor displacement concerns.
- What is the future of CNC machining?
The future of CNC machining will be shaped by smart technologies, hybrid manufacturing processes, and efforts to address ethical and sustainability concerns.
Conclusion
CNC taboo encapsulates the complexities, challenges, and ethical considerations associated with CNC machining. By understanding and addressing these taboos, businesses can optimize their CNC operations, improve product quality, and navigate the evolving landscape of modern manufacturing. Embracing responsible innovation and ethical decision-making will be essential for ensuring the continued growth and success of CNC technology in the future.
For further reading, consider visiting resources like the Society of Manufacturing Engineers (SME) for more insights on CNC technology advancements and best practices in the industry.
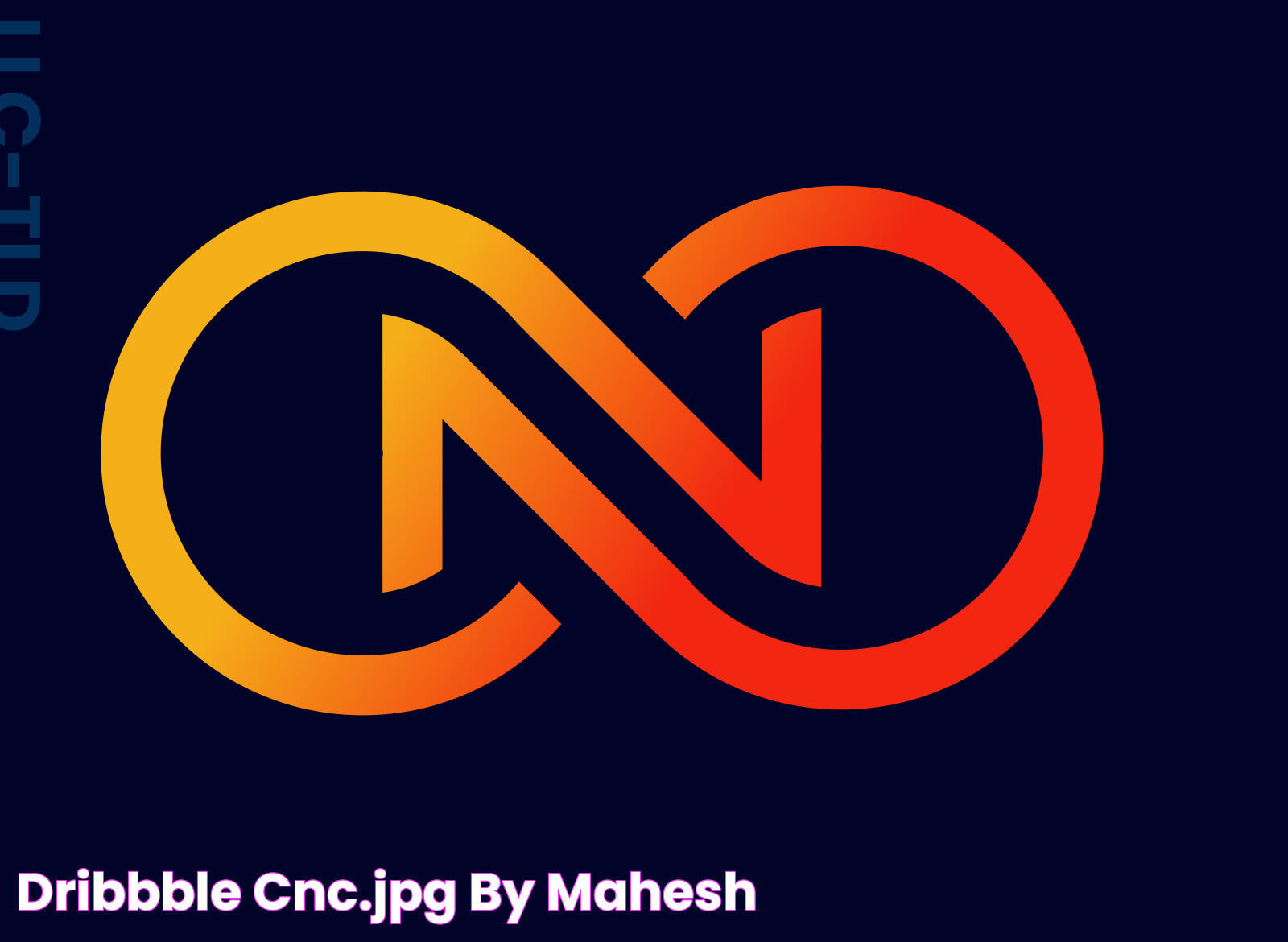
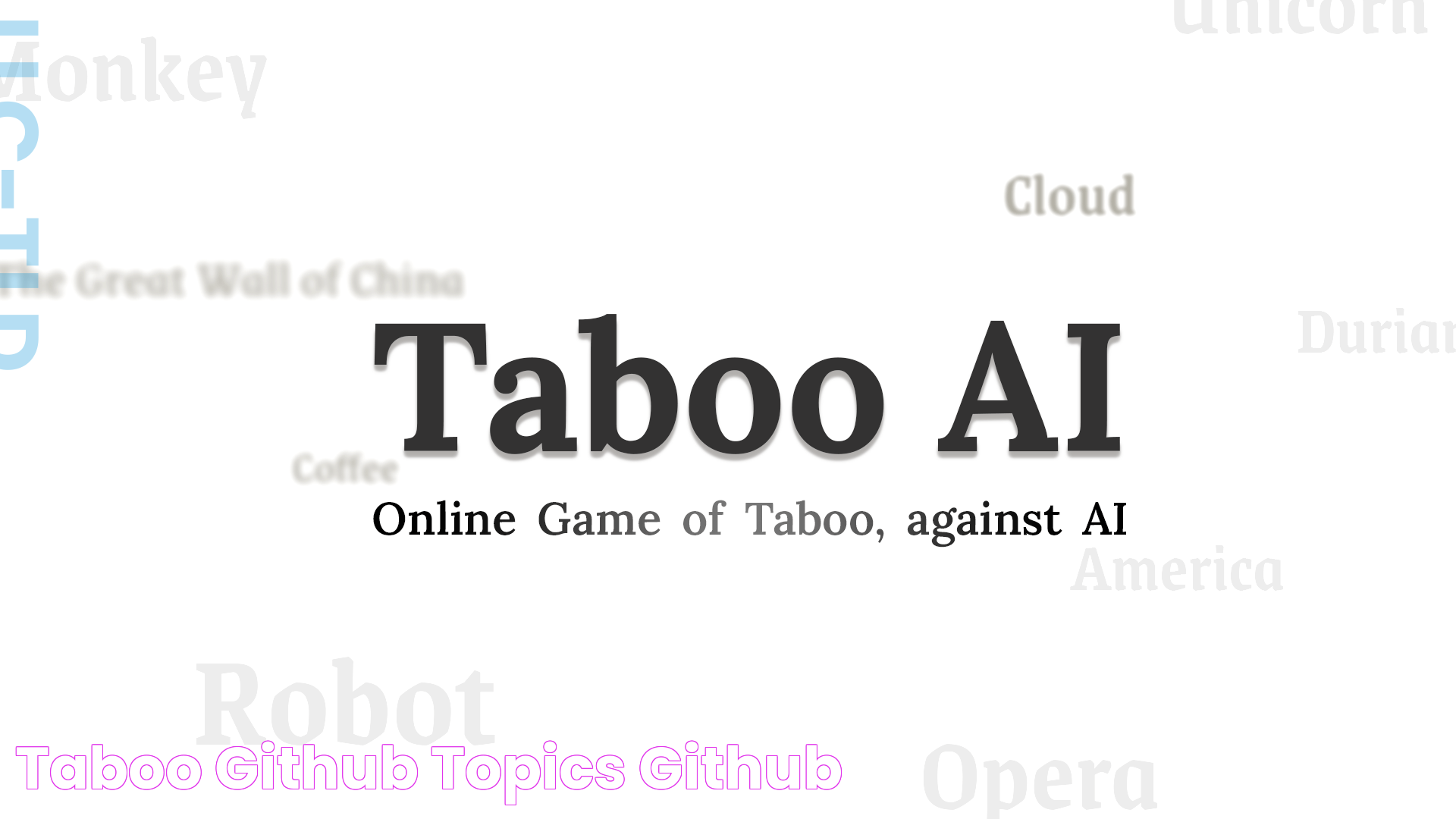